Transforming Shop Floor Operations
How Product Strategy helped transform outdated shop floor ops and eliminate paper waste for AJW Technique’s “NEO” initiative — and validated a new business.
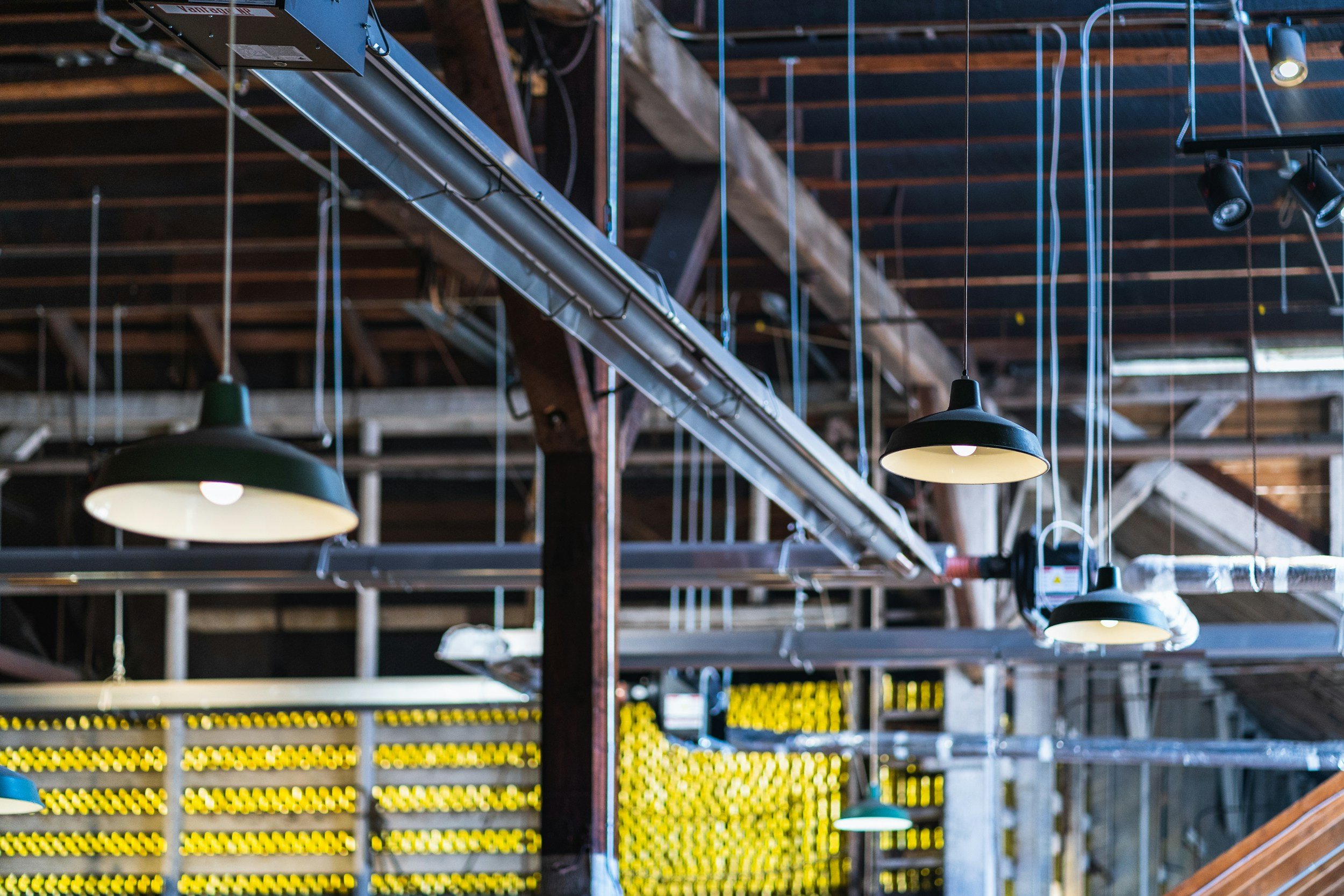
In a Nutshell
A large portion of the Aviation Industry are slow movers — large companies who are late adopters for new technology on the B2B side. AJW Technique decided it was time to modernize their shop floor, where workers repaired aircraft parts.
Overview
Workers on the warehouse shop floor at AJW technique relied on legacy systems — which slowed their work down due to un-intuitive workflows and an over-reliance on paper. As we worked with them we learned that the Aviation industry has skewed towards an older demographic. But now, young new hires and itching to get their hands on systems that will help them do their work better, not slow them down.
Role: UX & UI Designer, UXR
Skills: Product Design: from Validation to Launch.
Company: AJW Technique (Later: NEO
Timeline: Jan-Dec 2020 (Launched later in 2022)
-
My first large freelance project, I was referred after my work at Bombardier for the trouble-shooting platform. Already aware of the MRO (Maintenance, Repair and Operations) space and its challenges, I jumped right in to help Monica Badra (CTO) create a platform that would meet AJW’s business goals as well as pain points happening on the shop floor.
-
I was recommended by Rebecca Canterbury (then Elevate now Cision), who I had crossed paths with earlier in my career.
I worked independently with her leading the discovery, and later led the discovery alongside the CTO, reporting directly to the CEO. -
Figma
Research & Discovery
Google Venture’s Design sprint structures is one of our favourites to follow. Once we find out how the team might best succeed through clear role allocation, our output immediately becomes of higher quality, as well as more frequent.
Some of my sketches
User Interviews
The project had already started when I joined, so there already was a process in place for UXR. The CTO created an incubator crew of key roles that would help us build a solution that would help the entire shop floor (later, this was validated as a standalone business: NEO/NextGen Aviation.)
Interview Process:
One-on-one shadowing in the warehouse
Digital walk-throughs of their processes
Incubator crew interviews and user testing sessions
Design Process
Initial workflows were tested in one-on-one sessions and group sessions with the incubator crew.
As the prototypes reached completion, the CTO led presentations to the CEO & test groups.
Innovation in Legacy spaces always comes with change management, which was a key part of every step along the way.
Much of the process focused on parts inventory and repair, though Work order management and shipping and intake were also key steps.
The V1 prototypes contained many legacy-style requests, but as we progressed and practiced change management we were able to move away from requests to keep it like before, as we understood some interview candidates did not like the idea of change, and they started to understand that this would enable them to do less of the work they actually did not like doing, and more time on what matters.
Before:
V1:
After: The Final Prototypes (Vision)
Main Menu & Work Order
Parts Search (Inventory) and Bill of Materials needed for Work Order
Work Order Overview & Summary (Evaluation Intake Process)
Due to very early or late shifts, some workers wanted Dark Mode.